吨钢电耗下降34.5%!降本数百万!
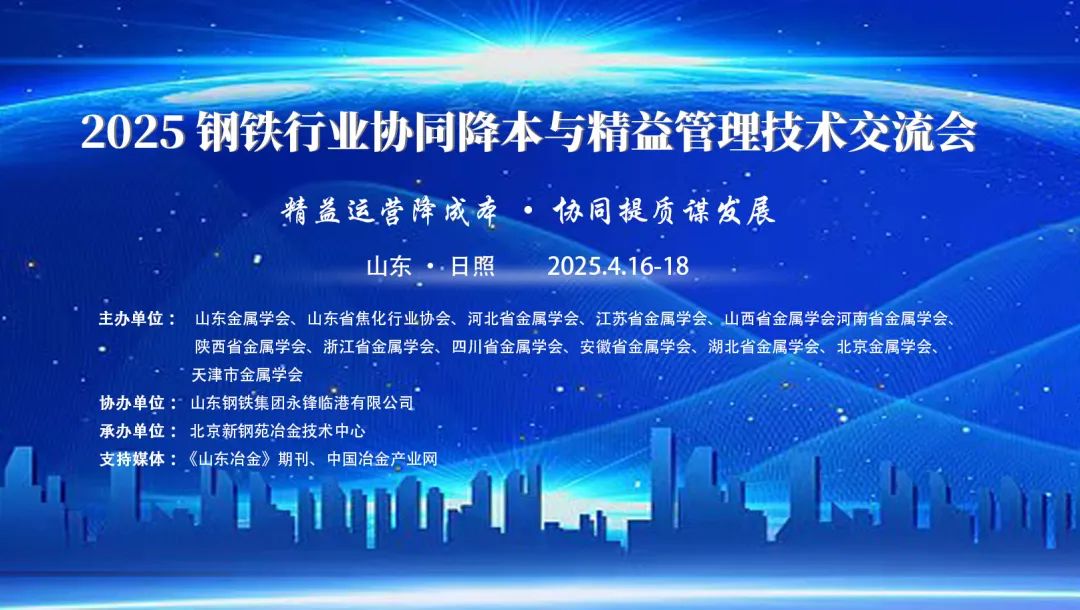
近期
中金公司炼钢厂全面启动
“精益用电降本攻关”
从优化生产到升级设备
四个维度精准管控能耗
近一个月
吨钢电耗同比下降34.5%
预计年均可减少电费支出数百万元
助力企业降本增效与可持续发展
实现双赢
科学调度,优化生产组织
中金公司炼钢厂以“时间换效益”,通过精细化生产调度降低能耗。一方面,实施错峰生产策略,AOD炉在用电高峰时段提高出钢温度,缩短精炼通电时间,能有效减少峰段电耗;调整连铸机开机时间,避峰生产,最大化利用谷段电价优势。另一方面,推进协同运行机制,推行连铸机与LF炉配套生产模式,严格执行停机切换间隔20分钟以上,避免公辅系统重复启动,有效降低需量电费。
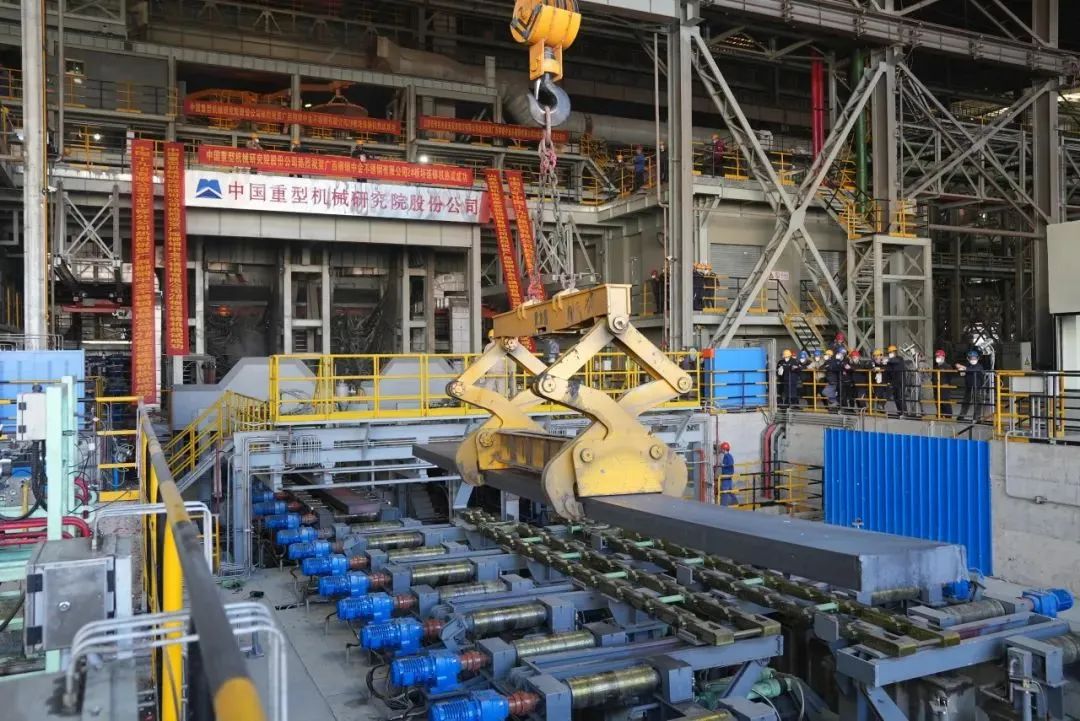
调整连铸机开机时间,避峰生产,降低需量用电
智能调控,升级设备能效
技术革新是节能降耗的核心驱动力。中金公司炼钢厂通过设备改造与智能化升级,实现“精准控能”。在变频节能方面,除尘风机按冶炼阶段分频运行,峰段散点除尘自动关闭;平车、制冷器等设备加装变频控制系统,实现能耗降低30%。此外,中金公司炼钢厂将LF炉2台水泵更换为160kW高效变频泵,运行功率降低至100kW,年节电量超20万度。同时,厂房照明实施分区分时控制,配电室空调与室温实现联动控制,减少了无效能耗。
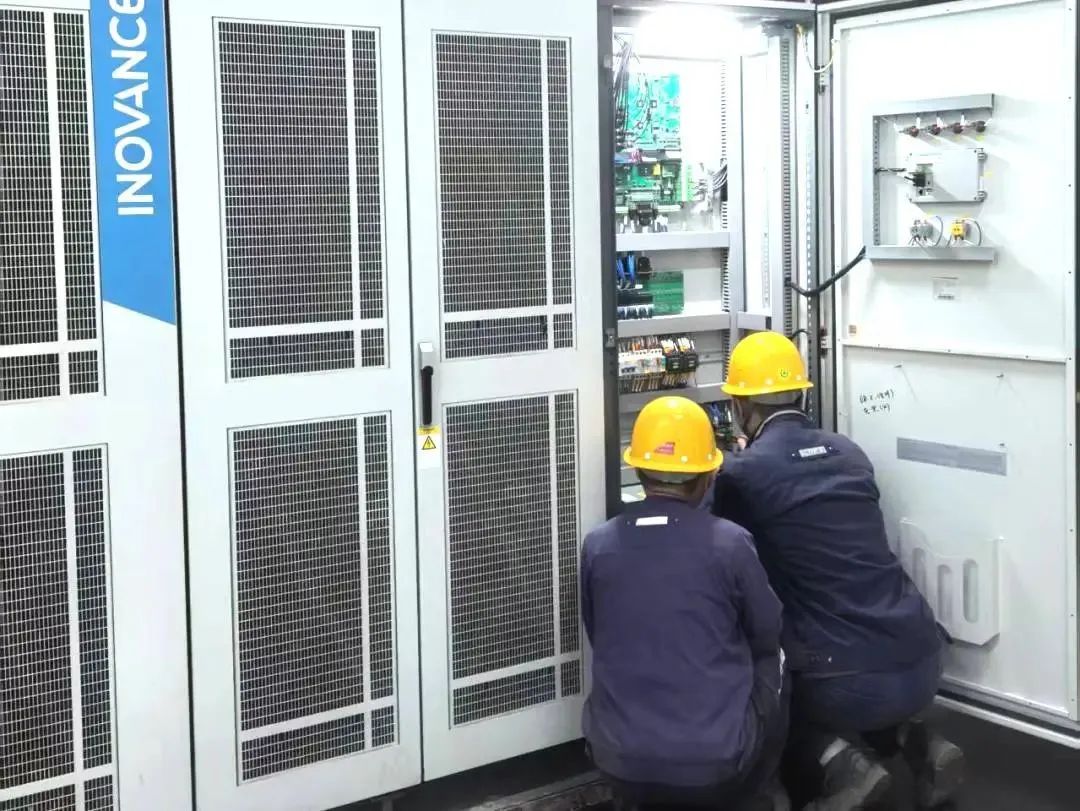
技术员对设备进行维护
全员行动,规范用电行为
节能降耗,全员参与。中金公司炼钢厂通过制度约束与文化引导,将节能理念融入日常操作。制度建设上,建立“人走电断”检查机制,生产设备随用随启,减少待机能耗。作业时间安排上,石灰上料、非生产行车运行、设备试机等作业集中安排至电价谷段,避开峰段高成本。设备运维管理上,液压站、加油设备严禁峰段进行非必要操作。
数据赋能,强化精细管理
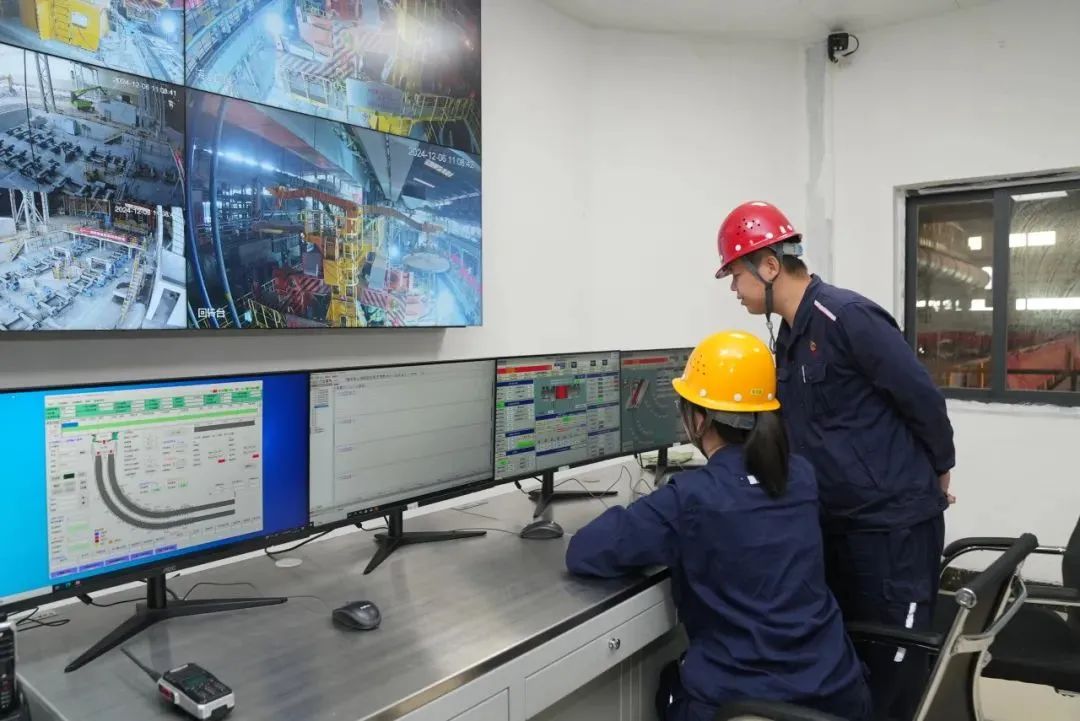
技术人员分析实时生产数据
依托信息化手段,中金公司炼钢厂构建“全流程能耗监控体系”,实现用电管理透明化、科学化。通过实时采集重点设备能耗数据,系统自动核查节电措施执行效果,做到实时监测。各区域用电量独立计量,每日生成分析报告,针对峰段用电超30%的用电工序进行定向整改,达成动态预警;基于大数据分析不断优化生产节奏,将峰段用电占比目标控制在30%以内。
来源:柳钢集团

